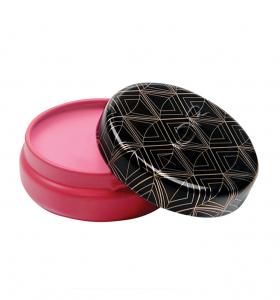
Raw Materials
The main component of a tin box is, of course, tinplate. Tinplate is a thin sheet of steel that has been coated with a layer of tin on both sides. This coating helps to prevent rust and corrosion, making tinplate the ideal material for food and other products that need to be protected from the elements. Tinplate is also highly malleable, allowing it to be easily shaped and formed into the desired box shape.
Apart from tinplate, other raw materials that are essential in the production of a tin box include:
1. Steel sheets: These are used as the base material for the tinplate and are made of low carbon steel. The steel is rolled into thin sheets and then coated with a layer of tin.
2. Lacquer: Once the tinplate is formed, it is coated with a layer of lacquer on both sides. This provides a protective barrier between the tin and the contents of the tin box, preventing any adverse reactions.
3. Printing inks: To give tin boxes an attractive design, they are printed with colorful and eye-catching designs. Printing inks are used for this purpose, and they are specially formulated to adhere to the lacquered surface of the tinplate.
4. Adhesives and sealants: These are used to seal the joints of the tin box and ensure that it remains airtight and leak-proof.
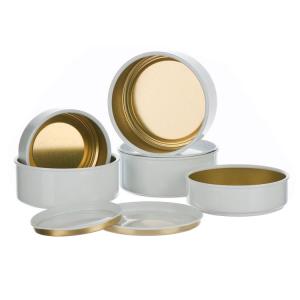
Production Process
The production of a tin box involves several steps, each of which is crucial to ensure a high-quality, durable product.
Step 1: Cutting the tinplate
The first step is to cut the tinplate into the desired size and shape using specialized cutting machines. The sheet is cut into small pieces that can be easily handled during the rest of the production process.
Step 2: Forming the tinplate
Next, the tinplate is passed through a series of rollers to form it into the desired shape and size. This process is known as deep drawing, and it is done using a machine called a press. The press uses a combination of pressure and heat to mold the tinplate into the desired shape, such as a rectangular or round box.
Step 3: Coating with lacquer
Once the tin box is formed, it is coated with a layer of lacquer on both sides. The lacquer protects the tinplate from moisture and other elements that could cause corrosion. The lacquer is applied using a spraying machine and is then cured by passing the tin box through a heating chamber.
Step 4: Printing the design
After the lacquer has been applied, the tin box is ready to be decorated with a vibrant and attractive design. This design is printed on the box using specially formulated inks that adhere to the lacquered surface of the tinplate. The printing process is generally done using a rotary or sheet-fed printing machine.
Step 5: Assembling and sealing the box
The next step is to assemble the tin box. Assembling a tin box involves folding and fitting the different parts together, such as the lid and the base. This is done using specialized machines that use adhesives and sealants to ensure that the box is airtight.
Quality Control
At every stage of the production process, quality control measures are implemented to ensure that the tin boxes meet the necessary standards. The quality control process involves visual inspection, as well as testing to check for strength, durability, and airtightness. Any defective tin boxes are immediately rejected and sent for recycling.
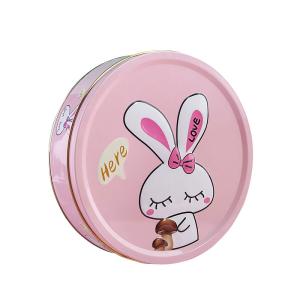
Packaging and Shipping
Once the tin boxes have been inspected and approved, they are packaged, ready for shipping. The packaging process involves wrapping the tin boxes in protective material and placing them in cardboard boxes for safe transportation. Tin boxes can be shipped worldwide, using various transportation methods, including air, sea, or land.
Recycling of Tin Boxes
One of the significant advantages of tin boxes is that they are highly recyclable. This means that they can be melted down and reused to create new products. The recycling process for tin boxes involves:
1. Sorting: The tin boxes are sorted according to the type of metal used.
2. Shredding: The tin boxes are shredded into smaller pieces.
3. Melting: The shredded pieces are then melted in a furnace.
4. Separation: The melted metal is separated from impurities such as labels, paint, and lacquer.
5. Rolling: The purified metal is then rolled into thin sheets, ready to be used again.
Huaiyang Metal Manufacture Co., Ltd was founded in 2013 and is a professional company that produces various tin boxes, metal boxes, and food cans. The company adheres to the business philosophy of "integrity, quality, efficiency, innovation, and service" and is moving towards the global market.
We have a production area of 20000 square meters and over 200 skilled workers. There are over 1000 sets of existing molds. 20 automated production lines. With a monthly production capacity of over 5 million pieces, we are able to promise our customers "high-quality products, excellent service, competitive prices, and timely delivery.". Specifically, the main products are as follows: biscuit boxes,coffee cans,candy boxes,candle cans,Watch case,Chocolate box,Stationery box,Storage tank,Cosmetic box,Mint box, etc. With the effective implementation of the ISO9001 quality management system, HY can ensure efficient production and high-quality products that meet Food grade requirements,RoHS,etc.
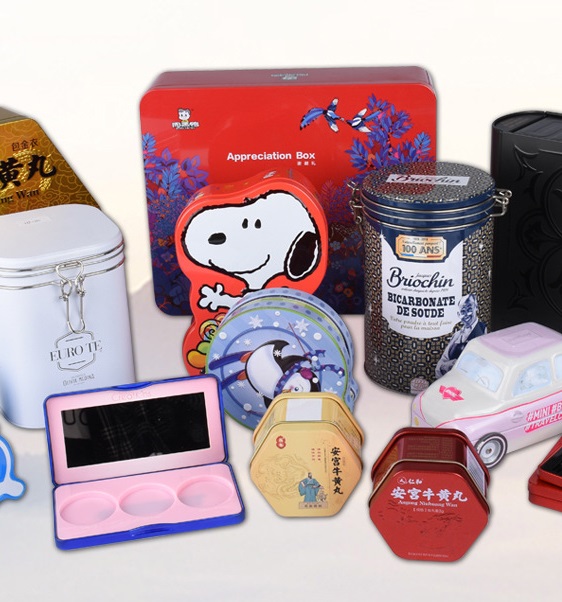
Related issues:
What are the advantages of a tin box?
Huaiyang Metal Manufacturing believes that tin boxes have many advantages and benefits:1. Durability: Tin boxes are highly durable and can withstand wear and tear.
2. Corrosion Resistance: Tin boxes are highly resistant to corrosion and rust, making them ideal for storing food and other items.
3. Recyclability: Tin boxes are 100% recyclable, making them an environmentally friendly choice.
4. Versatility: Tin boxes come in a variety of shapes and sizes, making them suitable for a wide range of applications.
5. Cost-Effective: Tin boxes are relatively inexpensive compared to other packaging materials.
Can tin box be recycled?
Yes, tin box can be recycled. Tin is a type of metal that can be recycled and reused. Most recycling centers accept tin boxes and cans for recycling.How diverse are the colors and patterns of tin box?
Tin box come in a wide variety of colors and patterns. They can be found in solid colors such as black, white, red, blue, green, yellow, and pink, as well as in a variety of prints and patterns such as stripes, polka dots, floral designs, and more. Some tin boxes even feature intricate designs and artwork.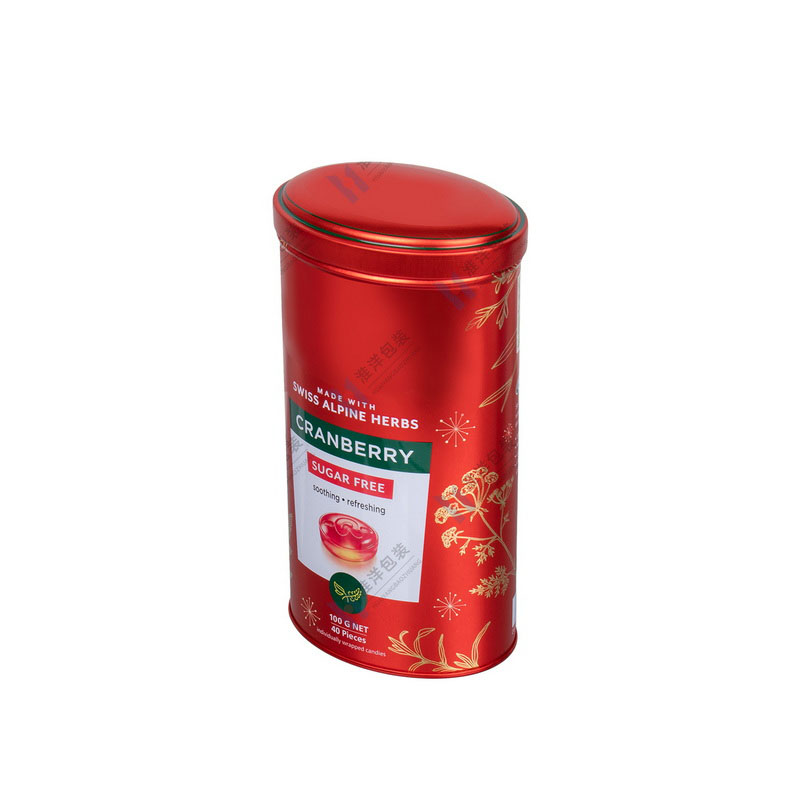